Ideal Practices for Effective Tank Welding Inspection Processes
Ideal Practices for Effective Tank Welding Inspection Processes
Blog Article
The Essential Duty of Tank Welding Examination in Ensuring Structural Stability and Safety Compliance in Industrial Applications
In the realm of industrial applications, tank welding assessment arises as a critical element in protecting architectural integrity and guaranteeing compliance with safety policies. Using a mix of strategies such as aesthetic evaluations and advanced testing techniques, these examinations serve to recognize and mitigate potential defects before they intensify into substantial risks.
Value of Tank Welding Evaluation
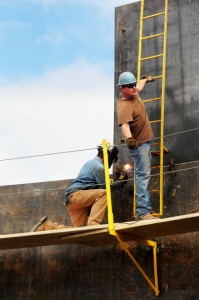
Making sure conformity with sector standards and laws is one more significant element of tank welding evaluation. Regulative bodies mandate stringent guidelines for the building and construction and maintenance of tank, and complete evaluations assist organizations comply with these needs. Non-compliance can result in extreme penalties, consisting of penalties and closures, even more stressing the requirement for extensive examination procedures.
In addition, container welding inspection plays an important function in keeping functional performance. Normal assessments can identify possible issues prior to they intensify, helping with prompt repair work and minimizing downtime. This proactive approach not just boosts security yet likewise contributes to cost savings in the lengthy run. In summary, the value of storage tank welding evaluation depends on its capability to protect public health and wellness, protect the setting, and ensure conformity with governing structures.
Secret Inspection Methods
Reliable tank welding inspection depends on a range of essential strategies that guarantee thorough assessment of weld top quality and architectural stability. Amongst the most common techniques are visual examination, ultrasonic testing, radiographic screening, and magnetic particle screening - Tank Welding Inspection. Each method uses unique benefits in analyzing various elements of the weld
Visual evaluation acts as the very first line of defense, enabling inspectors to identify surface area flaws, abnormalities, or variances in the weld bead. Ultrasonic screening employs high-frequency acoustic waves to spot inner problems, such as fractures or voids, providing a thorough assessment of weld honesty. This technique is especially reliable in identifying issues that may not show up on the surface.
Radiographic screening utilizes X-rays or gamma rays to generate photos of the welds, exposing internal stoppages and providing a permanent document for future reference. This technique is highly reliable for essential applications where the risk of failing should be minimized.
Lastly, magnetic fragment screening is utilized to determine surface area and near-surface problems in ferromagnetic materials. By using electromagnetic fields and fine iron fragments, inspectors can identify stoppages that may compromise the structural honesty of the storage tank. Together, these techniques form a durable structure for making sure top notch welds in commercial resource applications.
Conformity With Safety Requirements
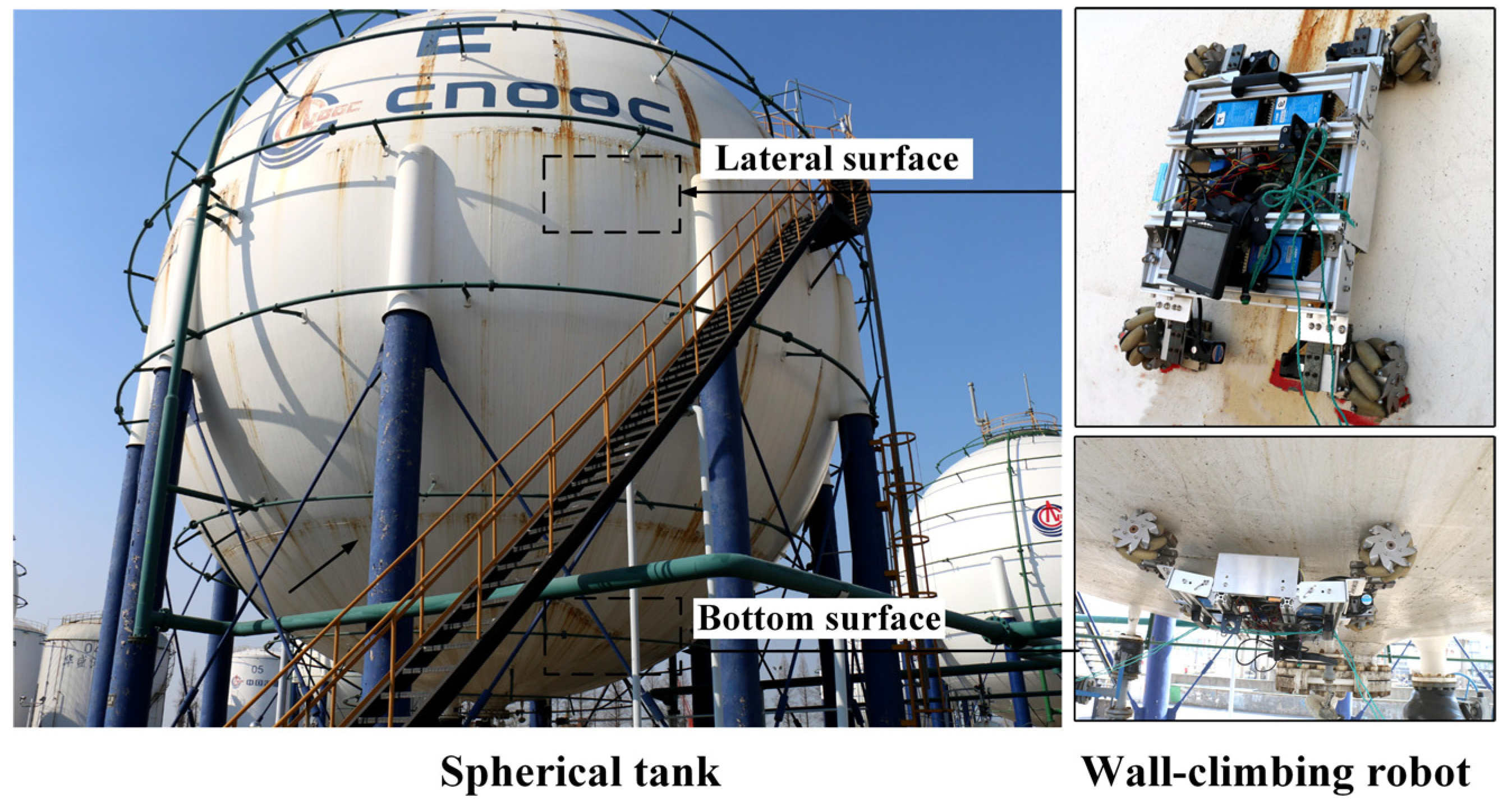
Routine inspections play a crucial function in ensuring conformity by determining prospective failings or inconsistencies from suggested standards. Assessors are trained to examine weld high quality, verify product requirements, and analyze the overall architectural integrity of storage tanks. Their knowledge is important in making sure that welding processes fulfill the required safety and security standards.
Additionally, compliance with safety requirements not only secures workers but additionally safeguards the atmosphere from possible risks such as leaks or tragic failings. Organizations that focus on safety compliance are better positioned to minimize threats, improve operational efficiency, and foster a society of safety within their labor force. In recap, keeping strenuous compliance with security criteria is essential for the effective procedure of tank welding activities in industrial setups.
Benefits of Normal Evaluations
Routine evaluations are indispensable to keeping the architectural honesty and safety of more helpful hints welded storage tanks. These assessments provide a methodical method to determining prospective flaws or weaknesses in the welds, guaranteeing that any concerns are resolved before they rise right into substantial failings. By carrying out routine analyses, companies can discover corrosion, fatigue, and various other forms of damage that might endanger container performance.
Moreover, constant examinations add to conformity with sector regulations and criteria. Following these standards not only mitigates legal threats but also boosts the organization's online reputation for safety and security and integrity. Routine assessments promote a proactive safety and security society, encouraging workers to identify and prioritize the significance of equipment stability.

Study and Real-World Applications
Situation research studies and real-world applications illustrate the substantial influence of reliable storage tank welding examination practices. Complying with the implementation of rigorous welding examination procedures, including aesthetic and ultrasonic screening, the center identified vital imperfections in weld seams that can have led to devastating failures.
Similarly, a water treatment plant applied a detailed evaluation program for its container welding operations - Tank Welding Inspection. By incorporating non-destructive screening approaches, the plant was able to detect early indications of corrosion and fatigue in weld joints. This prompt intervention expanded the life expectancy of the storage tanks and made certain compliance with safety laws, hence protecting public health
These study highlight the significance of normal and systematic tank welding evaluations. By prioritizing these practices, markets can reduce dangers, enhance structural honesty, and guarantee conformity with safety standards, ultimately resulting in improved functional efficiency and decreased liabilities.

Conclusion
In conclusion, container welding assessment is an essential element of preserving structural stability and safety and security in industrial applications. Utilizing numerous assessment strategies ensures early detection of potential problems, therefore preventing disastrous failures.
Report this page